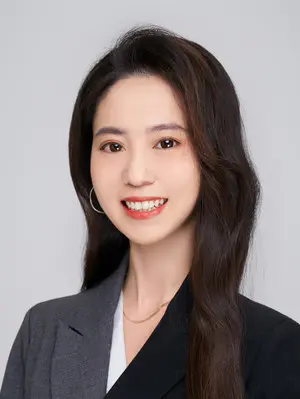
Ms. Katelyn Xue
Sr. Manager of Data Center,HJT EXPO
Phone | +86 21 6323 2733 |
---|---|
Fax | +86 21 6323 2733 |
katelyn.xue@hjtexpo.com | |
Address | 5th floor, World Trade Tower, 500 Guangdong Road, Huangpu District, Shanghai |
Recent advances in converting and bagmaking include advances in the production of battery film, developments in mono-material pouches and a multi-partner project to recycle big bags.
IMAGE: STARLINGER
Starlinger block bottom valve bags with 22% recyclate, are made on its Ad*StarKon SXneo line.
Despite a global war against single-use plastic shopping bags, demand for more durable bag products – such as those for packaging applications – remains high. Similarly, converters of film – into products as diverse as stand-up pouches and battery film – are also reporting technical advances.
Austrian packaging machinery supplier Starlinger showed a number of bagmaking solutions at Interpack 2023 recently.
One example was a project involving Starlinger, big bag manufacturer LC Packaging, PET recycler PRT – part of Alpla Group – and Croatian recycler Velebit. Together, they will jointly implement a closed loop for big bags made of polypropylene (PP) later this year.
The big bags, which PRT uses to transport and store input materials and the rPET granules produced from them, are recycled into rPP pellets by Velebit on a Starlinger recycling plant. LC Packaging mixes the recycled pellets with virgin material and produces tape fabric which is converted to rPP big bags. The finished big bags are then supplied again to PRT.
To make PP big bags, Starlinger processes recycled PP – also from post-consumer waste – on its production lines.
“Our customers are already producing big bags with recycled PP,” said Angelika Huemer, managing partner at Starlinger. “If the quality of the recycled material is good, high proportions of recycled content in this type of heavy-duty packaging, which has to fulfil special requirements, are no problem.”
With the technology to make big bags from PET – as an alternative to PP – Starlinger can offer manufacturers in this packaging segment a solution for a closed packaging cycle. When properly recycled, rPET achieves properties like virgin resin and can be used up to 100% for the making packaging. Starlinger now allows a way to produce big bags from 100% recycled PET.
Also at the show, a new Starlinger sack conversion line, MultiKon KXservo, was seen producing IC*Star sacks. In the IC*Star production process, the cut sacks run through a welding device in which a coated sealing strip is welded onto the bottom of the sack in a continuous process using hot air in order to close it. IC*Star sacks are characterised by material-saving production, high strength and low packaging weight, says the company.
Cement sack
Earlier – at last year’s K2022 – the company unveiled what it called the “cement bag of the future”.
It says the block bottom valve bags, made of woven plastic, are not only a tear- and moistureresistant packaging for dry bulk goods but are also becoming an increasingly sustainable alternative in the sector.
At the show, it produced its Ad*Star block bottom valve sacks with 22% recycled content on its new sack conversion line, Ad*StarKon SXneo.
“We want to show that it is possible to use recycled material in woven plastic packaging, which is manufactured in a complex process, without having to accept a loss of quality,” said Hermann Adrigan, Sales Manager at Starlinger.
In addition, Starlinger’s GripTec technology can increase the coefficient of friction on the bag surface to reduce slipping of stacked bags. This reduces the risk of personal injury from bags slipping down, and saves tonnes of bulk material and packaging, says the company.
Battery growth
New Era Converting Machinery says it has become more involved in battery production as the industry has grown.
IMAGE: NEW ERA
New Era says it provides custom-designed solutions for the battery industry.
“We provide custom-designed solutions for the industry,” said Paul Lembo, executive vice president at New Era. “We design and manufacture pilot and production equipment for numerous battery industry material applications – including anode and cathode coating, separator materials and vibration dampening/thermal foams such as polyurethane and silicone.”
It says it has extensive web handling experience with most materials that can be handled in a roll-to-roll format – including coating, laminating, calendering and general web handling.
“Our web handling, coating and laminating experience has positioned us well for this period of battery development,” said Lembo. “Our engineers are skilled in partnering with customers to provide web handling equipment that is tailored to their specific converting needs.”
In a recent collaboration, it helped Coreshell Technologies with a prototype demonstration – which showed the scalability of Coreshell’s battery coating technology, allowing it to be seamlessly integrated into the automobile manufacturing process.
Coating control
BST says that its BST Coating Control system can also help to improve efficiency in the production of battery separator film.
The system automatically optimises web-running processes within a small footprint – combining intelligent control technology and precise measuring instruments with line or CIS camera technology.
“In battery production, the smallest deviations lead to rejects,” said Florian Kortekamp, project and business development manager at BST. “BST Coating Control delivers competitive advantage by increasing plant efficiency.”
Reliable real-time measurement of the coating layers reduces the number of line stops, it says. In combination with the Frame Guide web guiding system, it maximises control accuracy through robust edge detection via a central control unit and closed-loop image processing algorithms.
Thanks to continuous coating positioning, no further manual offset correction by the machine operator is required.
“The accuracy of the entire system is twice as high as that required by the industry,” according to Kortekamp.
This is the second generation of Coating Control and provides live camera images of the coating as well as an intuitive user interface, says BST. The system detects minimal production defects and takes immediate action to reduce reject rates.
ICE show
The company showcased this – and a number of other technologies – at the recent ICE show in Germany – including web guiding, surface inspection, web monitoring, print inspection, register and coating control.
IMAGE: ICE
BST showcased its TubeScan quality assurance system at the recent ICE show.
“With our high-precision system solutions, we increase the efficiency and sustainability of all web processing operations,” said Jörg Westphal, executive vice president of the flexible materials business unit. “We know the current challenges of the markets well – and understand our customers’ machines and processes in depth.”
At the show, BST presented iPQ-Surface, a surface inspection system for quality assurance in material production. While it was used to inspect transparent and opaque films, it can also be used for battery cell production or cold seal applications.
The iPQ-Surface combines state-of-the-art camera technology with multiplex lighting to reveal small defects in a compact installation space. Simultaneously, the system can be adapted to the respective application and offers a modular concept for lighting and camera options. As well as coordinated hardware components, it offers an intuitive user interface that is tailored to the user.
In addition – for print inspection – BST presented TubeScan, for quality assurance in material finishing. The system enables a cost-effective entry into 100% print image inspection and has many illumination options. Since last year, it has been available for web widths of up to 1,700 mm. The latest development is the reliable inspection of variable data, such as barcodes and QR codes, at web speeds f up to 500m/min, enabling maximum efficiency in label web converting, says BST.
Wide-format bag
Dow, in collaboration with machine manufacturers Windmoller & Holscher (W&H) and B&B, has developed a recyclable, wide-format MDO-PE bag – which uses only polyethylene (PE) and a minimal layer of EVOH to achieve its aims.
IMAGE: DOW
Dow, W&H and B&B have developed a recyclable MDO-PE bag aimed at petfood packaging.
The product is aimed at the pet food packaging market. The challenge for recyclable pet food packaging has been finding technologies that maintain the efficiency of the packaging’s production and its final qualities – while relying only a single material.
“Packaging recyclability is a challenge that no one company can do alone,” said Romain Cazenave, packaging EMEA marketing director at Dow Packaging & Specialty Plastics. “Dow’s Elite, Innate and Affinity resins and sealants have helped realise the next generation of recyclable packaging.”
The film was produced on a W&H Varex II machine with inline MDO. It has a final web width of 2 x 1260 mm and is optimized to reduce material wastage during production. It was then laminated at industrial scale before being made into bags on B&B’s side-gusseted SFB bag machine. This produced 80 bags per minute, which is comparable to multi-material PET/PE structures.
Mono-material pouch
W&H – in collaboration with other partners – has also developed a mono-material PE pouch with similar properties to multi-material laminated pouches.
The new pouches use the latest polymers, inks, coatings, adhesives and converting technology, say the partners – which also include ExxonMobil, Henkel, Kraus Folie and Siegwerk.
The development allows for pouches with a high oxygen barrier, package integrity and shelf-appeal. It produces an almost colourless recyclate after the removal of printing ink and the oxygen-barrier coating layer.
To produce a colourless recyclate, the delamination and removal of the printing ink and coating from the laminate structure is crucial. Here, Siegwerk’s delamination/deinking primer technology was applied on a W&H Miraflex II – a flexo printing press with a downstream unit.
The oxygen-barrier properties are achieved through using Loctite Liofol BC 1582 RE – a one-component barrier coating from Henkel – and Cirkit OxyBar BC 1582 from Siegwerk. The coating can be applied on both flexo and gravure presses at industrial machine speeds on various substrates, giving excellent transparency. Its compatibility with recycling has been confirmed by Cyclos HTP.
Packaging integrity is achieved using ExxonMobil’s latest generation of materials such as Exceed S and Exceed XP, in combination with Exact materials in the sealant layer. The MDO-PE films had been developed by ExxonMobil and Kraus Folie, using ExxonMobil HDPE and Enable materials, and produced on a Varex II extrusion line with an inline MDO unit.
PCR in bags
Borouge has developed a method to incorporate post-consumer recycled (PCR) content into PE-based heavy duty shipping sacks.
IMAGE: BOROUGE
Borouge and partners have developed a heavy-duty shipping sack with 30% PCR content.
New sacks are made from 30% PCR content – originally used in the same type of product – together with Borouge’s Borstar and Anteo PE grades.
Borouge worked with partners, Han King Plastic Machinery, Kunshan Golden Alliance, Shanghai Longstone and Shanghai Tianqiang to develop the closed-loop PE for heavy-duty sacks, with the aim of developing a sustainable solution with a lower carbon footprint.
Material from used sacks is recovered through waste collection streams, then mechanically recycled. The recycled resins are then incorporated – with virgin PE – to the end application.
“This circular solution enables multiple recycling cycles within the same application, which takes us a step closer towards a circular economy,” said Eddie Wang, senior vice president for Asia North at Borouge.
Source:Film and Sheet Extrusion (www.filmandsheet.com)
Key Words:#Foams, #Bagmaking, #Plastics, #PE, #Battery Film, #Materials, #Recycling, #Expo, #Exhibition, #Interfoam, #Vietnam, #Packaging
Sr. Manager of Data Center,HJT EXPO
Phone | +86 21 6323 2733 |
---|---|
Fax | +86 21 6323 2733 |
katelyn.xue@hjtexpo.com | |
Address | 5th floor, World Trade Tower, 500 Guangdong Road, Huangpu District, Shanghai |
Please browse vertically for better experience.